Understanding CNC Machines: The Future of Precision Manufacturing
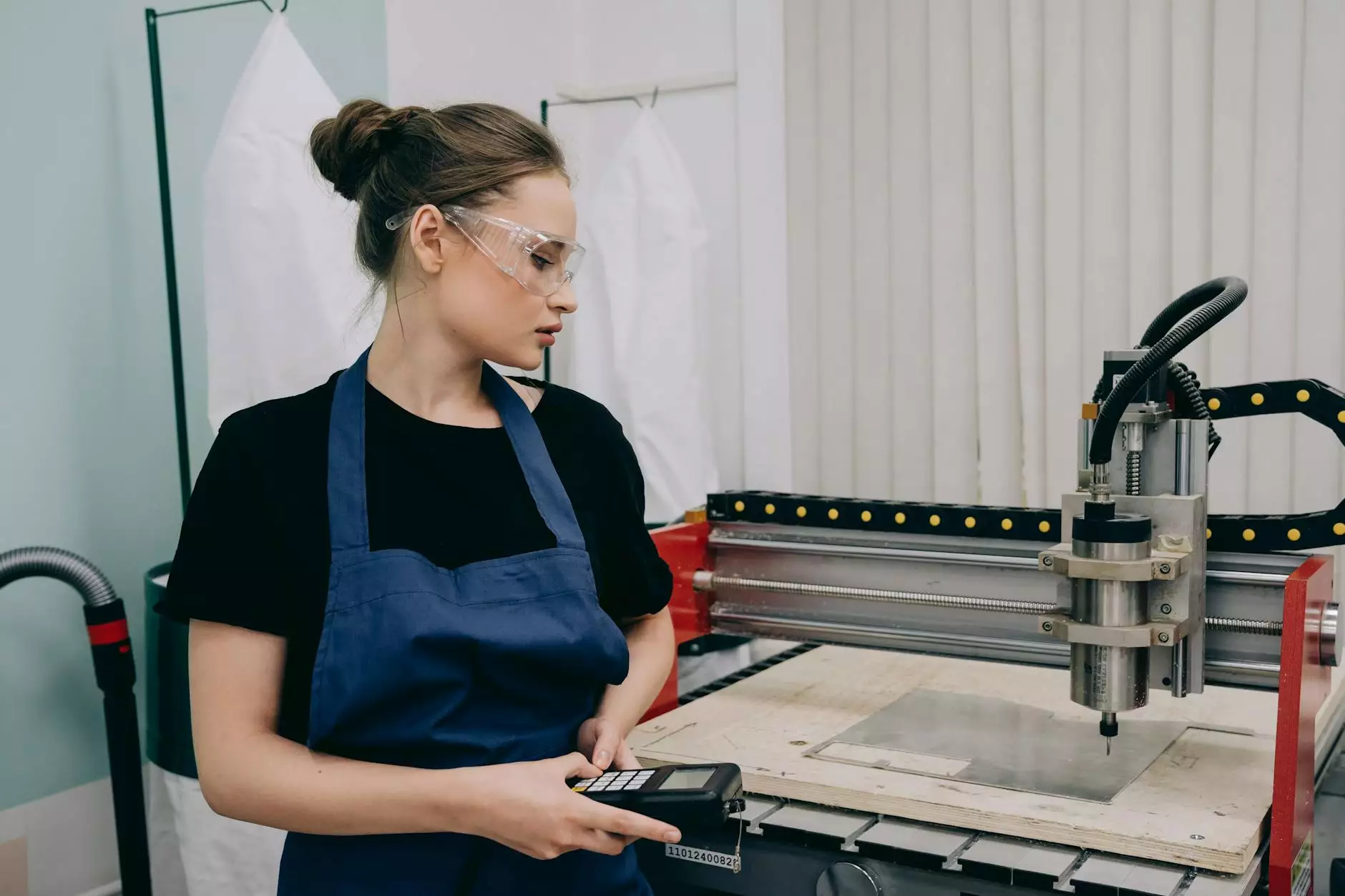
In today's fast-paced industrial landscape, CNC machines stand out as a cornerstone of modern manufacturing. These sophisticated tools are automated systems that utilize computer programs to execute precise commands with unparalleled accuracy. Unlike traditional machining methods that rely on manual controls such as handwheels and levers, CNC machines bring together cutting-edge engineering and revolutionary technology to produce consistent and high-quality outcomes. This article aims to provide a detailed understanding of CNC machines, their operational mechanics, programming, and their vast array of applications in various industries.
What Are CNC Machines?
CNC stands for Computer Numerical Control, which describes how these machines operate. CNC machines can be classified into several categories: lathes, mills, routers, plasma cutters, and more. Each type serves a specific purpose in the manufacturing process, making them incredibly versatile. They primarily utilize G-code, a programming language that dictates every aspect of the machining process, from the speed and feed rate to the movement paths of the cutting tools.
The Evolution of CNC Machining
The evolution of CNC machining has been a dramatic journey from traditional machining to today's advanced technology. Historically, machining was a manual process. Craftsmen operated machines using their skills to create parts by hand. As industry demands outgrew human capabilities, the need for automation emerged.
- Manual Machines: Operated by hand, these machines required extensive skill and were subject to human error.
- Mechanical Automation: Early automation techniques relied heavily on cams and levers, which improved precision but lacked the flexibility of modern systems.
- CNC Technology: The introduction of computers into the manufacturing process revolutionized production, enabling complex parts to be created with the push of a button.
How CNC Machines Work
The operation of CNC machines revolves around a three-step process: design, conversion, and execution. Here's a breakdown:
1. CAD Design
First, a part is designed using Computer-Aided Design (CAD) software. This software allows engineers to create detailed 2D and 3D models, specifying all dimensions and geometries. The CAD model serves as the blueprint for the subsequent manufacturing process.
2. CAM Programming
Next, the CAD design is converted into Computer-Aided Manufacturing (CAM) software. This software translates the design into machine instructions, generating the G-code that will steer the CNC machine during operation. This includes specifying the type of tooling, cutting speeds, and movements necessary for machining the part.
3. Machining Execution
Finally, the CNC machine receives the G-code and executes it. The machine moves along various axes (often including X, Y, and Z) to cut, drill, or shape the material according to the programmed specifications. This execution is incredibly precise—resulting in components that often exceed the tolerances achievable by manual methods.
Key Advantages of CNC Machining
An array of significant advantages comes with the adoption of CNC machining in industrial processes:
- Precision: CNC machines offer unparalleled accuracy, producing parts to exact specifications with minimal error.
- Consistency: Once a program is set, CNC machines can replicate the same process repeatedly, ensuring uniformity in production.
- Efficiency: Automated processes reduce labor costs and increase production speed, allowing manufacturers to meet higher demands.
- Complex Shapes: CNC machining can produce intricate geometries and complex designs that would be impossible with manual methods.
- Material Flexibility: These machines can work with a wide range of materials, including metals, plastics, and composites.
Types of CNC Machines
CNC machines come in various types, each tailored for specific applications:
CNC Milling Machines
CNC milling machines are used for cutting and shaping materials. They feature rotating cylindrical tools that remove material as the workpiece moves into the machine. These machines are versatile and can handle complex parts.
CNC Lathes
CNC lathes operate by rotating the workpiece against a stationary cutting tool. This process is ideal for producing cylindrical or spherical parts and is widely used in the automotive and aerospace industries.
CNC Plasma Cutters
CNC plasma cutters use a plasma torch to cut through conductive materials like steel and aluminum. They are essential for industries that require precise sheet metal fabrication.
CNC 3D Printers
3D printers represent a newer category of CNC machinery, focusing on additive manufacturing. They create parts layer by layer from materials like plastics and metals, allowing for rapid prototyping.
Programming CNC Machines
Programming is a critical component of CNC operations. The accuracy of the machining process relies heavily on the quality of the G-code generated. Programmers must understand both the software and the machinery to create effective programs.
G-code Basics
G-code gives CNC machines a series of instructions to follow. Here’s a glimpse of common G-code commands:
- G00: Rapid positioning – moves the machine to a location without cutting.
- G01: Linear interpolation – moves the machine while cutting at a specified feed rate.
- M00: Program stop – halts the operation.
- M03: Spindle start – enables the machine's spindle for operation.
Essential Skills for CNC Programming
To be a proficient CNC programmer, one must possess a variety of skills, including:
- Understanding of machining processes and equipment
- Proficiency in CAD and CAM software
- Mathematical skills for calculations involving angles and measurements
- Problem-solving abilities for troubleshooting programming issues
The Role of CNC Machinists
While computers drive CNC machines, qualified CNC machinists are crucial for operations. They ensure the machines are set up correctly, monitor the machining process, and perform maintenance as needed. Their expertise in interpreting G-code and understanding the mechanics of the machine allows them to enhance productivity and maintain quality.
Applications of CNC Machining
CNC machining has a broad spectrum of applications across various industries:
Aerospace Engineering
In aerospace, precision is paramount. CNC machined components must meet stringent tolerances for performance and safety, from structural frames to engine parts.
Automotive Manufacturing
The automotive industry utilizes CNC machines for producing complex parts such as cylinder heads, crankshafts, and chassis components, all of which require high precision.
Medical Devices
From surgical instruments to implants, CNC machining enables the production of intricate and reliable medical devices that must adhere to strict regulatory standards.
Consumer Electronics
CNC machining is fundamental in creating components for smartphones, computers, and other consumer electronics, where precision and quality are critical to function and aesthetics.
Future of CNC Machining
The future of CNC machining is poised for exciting advancements. Integration with technologies like Artificial Intelligence (AI), Internet of Things (IoT), and advanced robotics is expected to revolutionize operations. Key trends include:
- Smart Manufacturing: IoT integration will allow machines to communicate with each other, enhancing efficiency and reducing downtime.
- Advanced Materials: Continued development of new materials will expand the capabilities of CNC machines.
- Automation: The rise of automated CNC setups will streamline operations and reduce the need for manual intervention.
The Importance of Skilled Professionals
For CNC machining to reach its full potential, the industry must prioritize the education and training of skilled professionals. As technology evolves, so too does the need for machinists and programmers who can operate and maintain these highly advanced machines.
Investing in qualification programs, apprenticeships, and continuous training is vital for fostering a skilled workforce that can harness the power of CNC machining to drive innovation in manufacturing.
Conclusion
In conclusion, CNC machines have transformed the landscape of manufacturing, providing unparalleled precision and efficiency. The journey from manual machining to highly automated CNC systems has paved the way for innovations across numerous industries. Understanding the complexities of CNC machining—coupled with the importance of skilled professionals in this field—will lead to even greater advancements and applications in the future. As we move forward, CNC technology will continue to play a pivotal role in driving the productivity and effectiveness of modern manufacturing processes.
For further insights into CNC technologies, applications, and solutions, visit RoboCNC.