The Comprehensive Guide to Plastic Injection Molding Factories
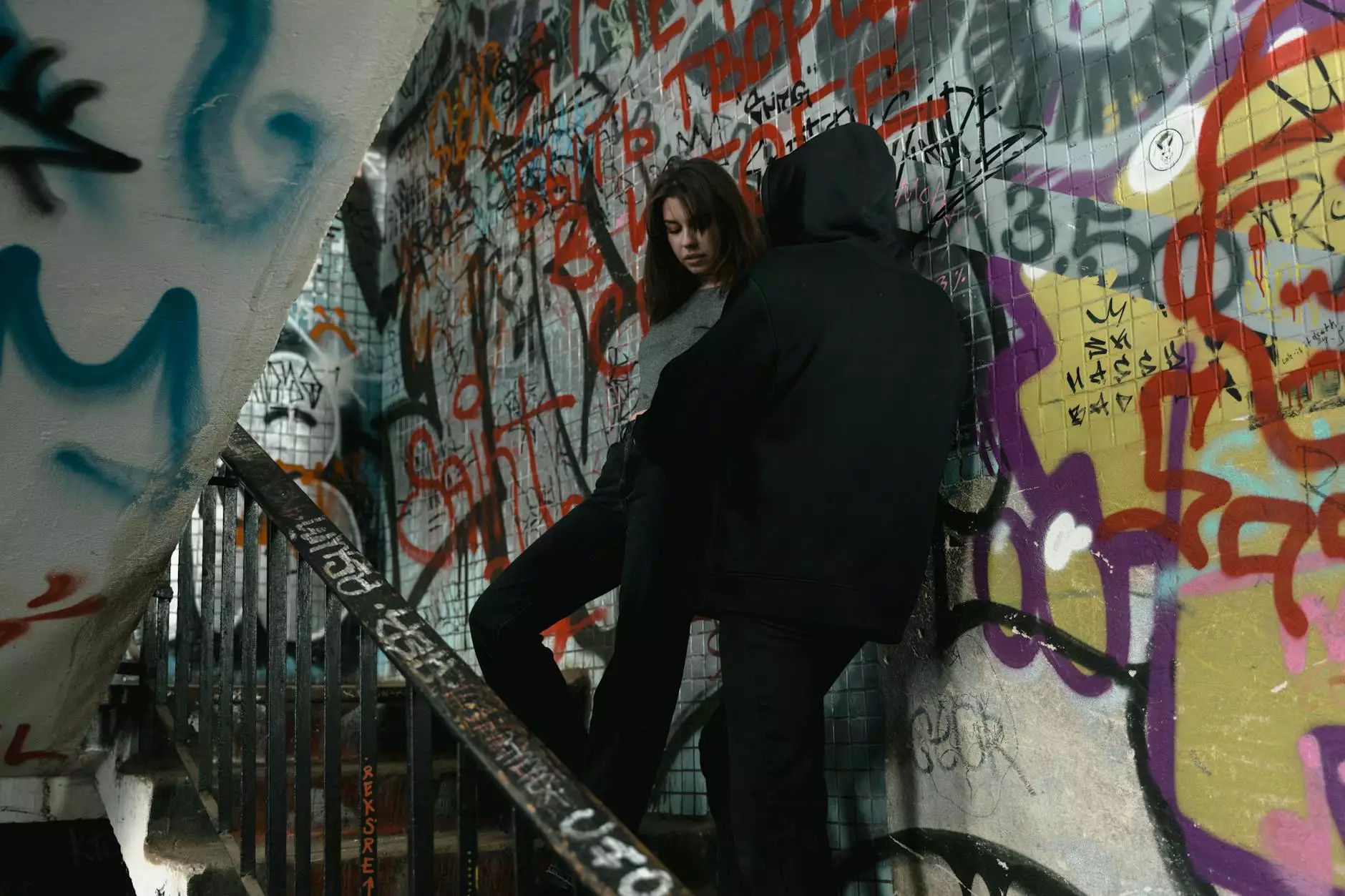
Plastic injection molding is one of the most significant processes in modern manufacturing, facilitating the creation of a vast array of products ranging from automotive components to household items. In this guide, we will explore the intricacies of plastic injection molding factories, including their operational mechanics, the benefits they provide to various industries, and their role in advancing manufacturing technology.
The Basics of Plastic Injection Molding
At its core, plastic injection molding is a manufacturing process for producing parts by injecting molten material into a mold. It is a highly efficient technique that enables the rapid production of large quantities of plastic components. The basic steps involved in the process include:
- Material Selection: Resin materials are chosen based on the intended application, heat tolerance, and other performance requirements.
- Melting the Plastic: The selected plastic resins are fed into a barrel and heated until they reach a molten state.
- Injecting into the Mold: The molten plastic is then injected under high pressure into a pre-designed mold cavity, where it cools and solidifies.
- Mold Opening and Part Retrieval: Once the part has cooled adequately, the mold opens, and the finished product is ejected.
The Role of Plastic Injection Molding Factories
Plastic injection molding factories play an essential role in the manufacturing landscape. They serve a multitude of industries including:
- Automotive: Producing components like dashboards, panels, and clips.
- Aerospace: Manufacturing lightweight parts that contribute to fuel efficiency.
- Consumer Electronics: Creating housings and components for devices like smartphones and tablets.
- Medical Devices: Producing critical components that meet stringent regulatory standards.
Industry Innovations Driven by Plastic Injection Molding
As technological advancements continue to evolve, plastic injection molding factories are at the forefront of innovation. Not only have they improved efficiency but they have also enhanced product quality through techniques such as:
- 3D Printing Integration: Integrating 3D printing technology to create prototype molds more rapidly.
- Smart Molding Technologies: Utilizing IoT and AI to monitor the molding process, improving precision and reducing waste.
- Biodegradable Plastics: Adopting sustainable practices by utilizing environmentally friendly materials.
Benefits of Using Plastic Injection Molding
The benefits of utilizing plastic injection molding factories are vast, offering efficiency, precision, and versatility:
1. Cost-Effectiveness
High-volume production with minimal labor and material waste leads to significant cost savings. Once the initial investment in tooling is made, the cost per unit decreases dramatically with increased production runs.
2. Design Flexibility
Plastic injection molding allows for the creation of complex geometries and designs that would be challenging to accomplish through other manufacturing methods. This flexibility encourages innovation in product development.
3. Rapid Production
The speed of the injection molding process means businesses can meet market demands quickly. With cycle times often measured in seconds, factories can produce large quantities in a fraction of the time compared to traditional methods.
Quality Assurance in Plastic Injection Molding Factories
Ensuring high quality is critical in any manufacturing process. Plastic injection molding factories implement rigorous quality control measures, including:
- Process Monitoring: Real-time monitoring systems track variables such as temperature and pressure to ensure optimal conditions.
- Material Inspections: Thorough checks of raw materials to verify compliance with specifications.
- Final Product Testing: Conducting tests on the finished products to confirm durability and functionality.
Challenges Faced by Plastic Injection Molding Factories
While plastic injection molding offers numerous advantages, factories face several challenges that require strategic solutions:
1. Tooling Costs
Designing and manufacturing molds can be expensive and time-consuming. Factories must balance the costs of high-quality molds with production demands.
2. Material Limitations
Not all plastics are suitable for every application, making material selection critical to the success of the finished product.
3. Environmental Concerns
With increasing focus on sustainability, plastic injection molding factories must adapt by using recyclable materials and minimizing waste.
The Future of Plastic Injection Molding Factories
The future of plastic injection molding factories looks promising as they embrace technological advancements. Innovations such as automation, artificial intelligence, and sustainable practices are set to redefine the manufacturing landscape:
- Automation: Increased automation in the factories will lead to improved efficiency and decreased labor costs.
- Smart Technology: Factories will deploy smart sensors and AI to enhance production monitoring and predictive maintenance.
- Sustainable Practices: Emphasizing the use of biodegradable plastics and recycling waste materials will align with global sustainability goals.
Partnering with a Reliable Plastic Injection Molding Factory
Choosing the right plastic injection molding factory can make a significant difference in your production capabilities. Look for a manufacturer that:
- Offers Comprehensive Services: From design to post-production support, a full-service factory can streamline your supply chain.
- Has a Proven Track Record: Research their history and customer reviews to ensure they have a reputation for quality and reliability.
- Utilizes Advanced Technology: Modern technology can lead to better product outcomes and increased efficiency.
- Complies with Industry Standards: Ensure that the factory meets all relevant safety and quality standards for your industry.
Conclusion
In summary, plastic injection molding factories are a cornerstone of the manufacturing industry, providing innovative solutions, cost-effective production, and high-quality products to various sectors. By staying abreast of emerging technologies and sustainability practices, these factories are not only meeting current demands but are also paving the way for future advancements in manufacturing.
To ensure your business thrives in a competitive landscape, consider partnering with a well-established plastic injection molding factory like Deep Mould. Their expertise in metal fabricators within the realm of plastic injection molding can enhance your production capabilities and support your goals for quality and efficiency.