Understanding the Role of a Precision Mold Supplier in Metal Fabrication
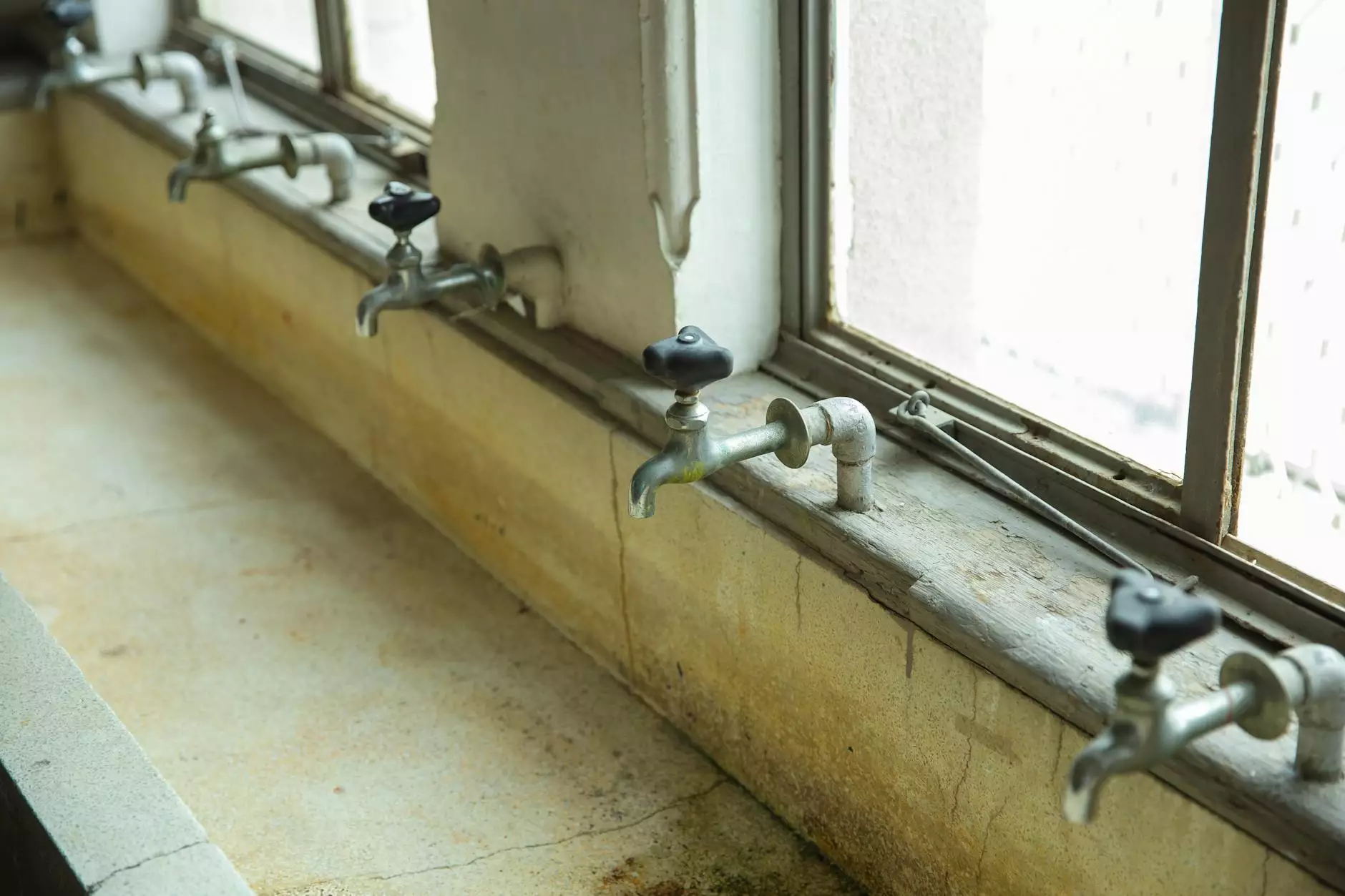
In the world of metal fabrication, the role of a precision mold supplier is invaluable. With the increasing demand for quality parts and components across various industries, businesses are on the lookout for suppliers who can deliver precision and excellence. At Deep Mould, we take pride in being a leading precision mold supplier, providing customer-centric solutions that enhance productivity and efficiency.
The Importance of Precision Molds
Precision molds are critical in achieving high-quality production outcomes. With industries ranging from automotive to consumer electronics relying on precise components, the demand for precision molds continues to grow. These molds not only help in shaping materials but also ensure consistency and accuracy in the final products. Here's why precision molds play a crucial role in manufacturing:
- Consistency: Precision molds guarantee uniformity in product dimensions, which is vital for assembly and functionality.
- Quality Assurance: They reduce the risk of defects, resulting in higher-quality end products that meet industry standards.
- Cost Efficiency: Investing in precision molds can significantly decrease waste and production costs, leading to greater profits.
- Scalability: High-quality molds enable companies to scale production without compromising on quality.
How Deep Mould Sets Itself Apart as a Precision Mold Supplier
At Deep Mould, we understand the nuances of being a precision mold supplier. Our commitment to quality and customer satisfaction is reflected in every mold we produce. Here are the key factors that set us apart:
1. Advanced Technology and Equipment
We invest heavily in state-of-the-art machinery and technology. This enables us to create precision molds that meet the exact specifications required by our clients. Our CNC machines and tooling processes are designed to deliver the highest accuracy and efficiency.
2. Expertise in Various Industries
Our team comprises experienced professionals with expertise across a range of industries, including automotive, aerospace, consumer goods, and medical devices. This diverse knowledge allows us to tailor our precision mold solutions to meet unique industry demands.
3. Custom Solutions to Meet Client Needs
At Deep Mould, we recognize that no two businesses are the same. We offer customized solutions that cater to the specific requirements of our clients. Whether it's a unique mold design or a specific material choice, we work closely with our clients to ensure their needs are met.
4. Rigorous Quality Control
Quality is at the forefront of everything we do. Every mold undergoes a stringent quality control process to ensure that it meets the required standards. We utilize various inspection techniques to guarantee precision in every detail.
The Manufacturing Process of Precision Molds
Understanding the manufacturing process of precision molds can help clients appreciate the level of detail and care that goes into each product. The typical process involves several key steps:
1. Design and Prototyping
The journey begins with the design phase. Using advanced CAD software, our engineers create intricate designs based on client specifications. Prototypes are often developed to test the design's feasibility and functionality before full-scale production begins.
2. Material Selection
The choice of material plays a vital role in the effectiveness of a precision mold. We offer a range of materials, including various steel grades, aluminum, and specialty alloys, ensuring that the molds meet the requirements of their intended use.
3. Machining and Fabrication
Once the design is approved and the materials chosen, the machining process begins. This involves cutting, shaping, and assembling the mold components using precision machinery. Our skilled technicians ensure that every part is crafted to the exact specifications.
4. Finishing Touches
The finishing stage includes polishing and surface treatment, which enhance the mold's durability and performance. This step is crucial for achieving the precision and smooth finish required for high-quality production.
5. Testing and Quality Assurance
After the molds are completed, they undergo rigorous testing to ensure that they perform as expected. We assess factors such as durability, precision, and functionality before delivering them to our clients.
The Benefits of Choosing Deep Mould as Your Precision Mold Supplier
Partnering with Deep Mould means choosing unparalleled quality and service. Here are some of the benefits our clients enjoy when they work with us:
- Expert Consultation: Our team offers expert advice, helping clients choose the best solutions for their needs.
- Quick Turnaround Time: We understand that time is of the essence in manufacturing, which is why we strive for efficiency without sacrificing quality.
- Support and Maintenance: Our relationship with clients doesn’t end at delivery; we offer support and maintenance services to ensure ongoing satisfaction.
- Competitive Pricing: We provide quality molds at competitive prices, helping businesses stay within budget while receiving excellent products.
Final Thoughts on Selecting a Precision Mold Supplier
Choosing the right precision mold supplier can significantly impact your production efficiency and product quality. With Deep Mould, you gain a trusted partner committed to delivering excellence. We invite you to explore our services and see how we can assist you in achieving your manufacturing goals.
Contact Us for More Information
If you’re ready to enhance your production with high-quality precision molds or have any questions, feel free to contact us. Visit our website at Deep Mould or reach out to our customer support team for tailored guidance.
© 2023 Deep Mould. All rights reserved.