Exploring the Benefits of Silicone Inks for Screen Printing
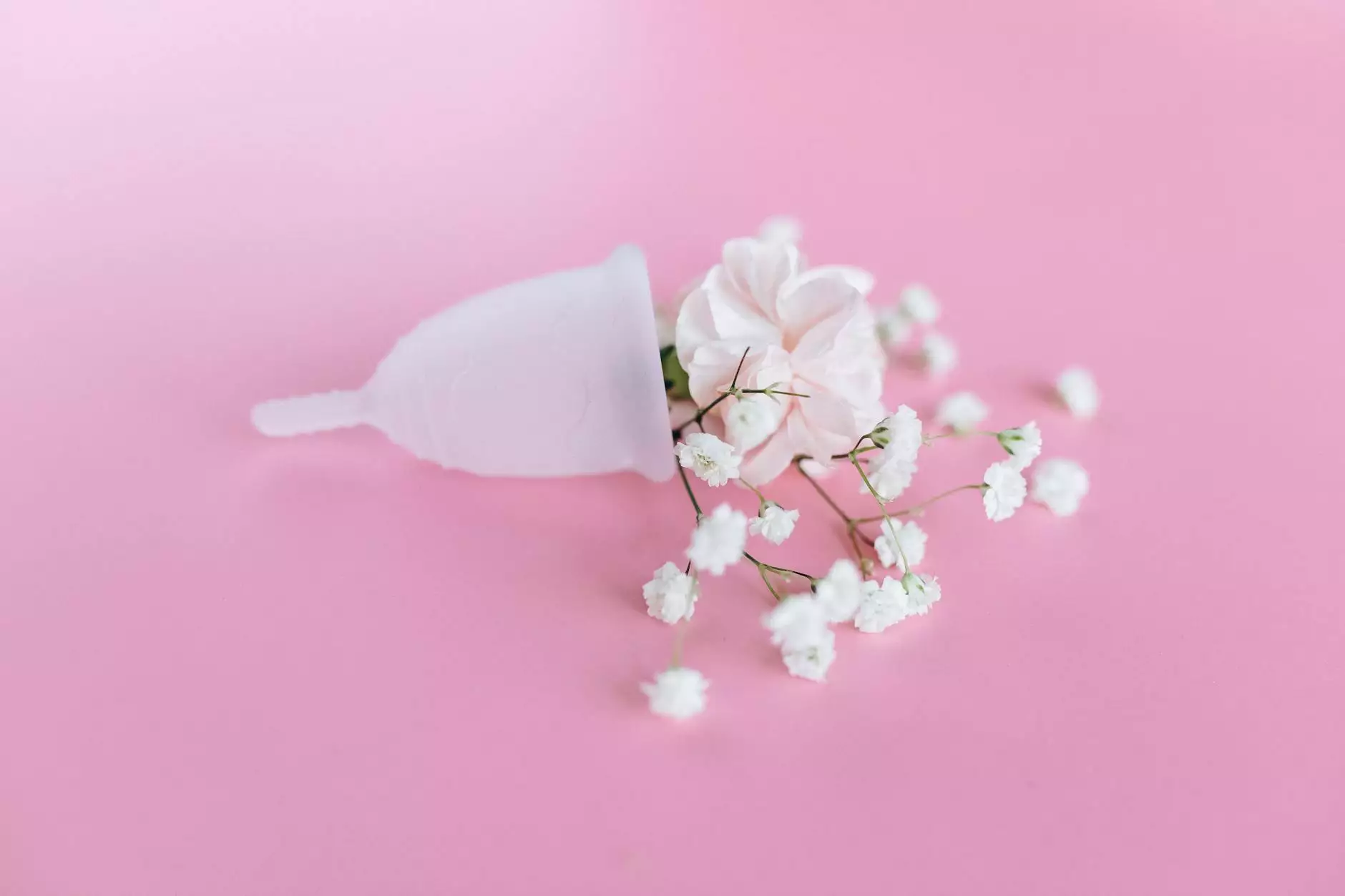
The world of screen printing is vast, filled with various methods, materials, and creative opportunities. Among the many advancements in this domain, one of the most significant innovations is the use of silicone inks for screen printing. These specialized inks have transformed the industry by offering numerous advantages over traditional inks. In this article, we will delve deeply into the characteristics, benefits, applications, and best practices for using silicone inks in screen printing.
Understanding Silicone Inks
Silicone inks are designed specifically for screen printing on textiles and other substrates. Unlike many conventional inks, silicone inks are composed primarily of silicone polymers, which impart unique properties that set them apart. Here are some key characteristics of silicone inks:
- Durability: Silicone inks are highly resistant to wear, fading, and cracking.
- Flexibility: These inks maintain their flexibility even after curing, allowing them to stretch without breaking.
- Environmental Resistance: Silicone inks are less susceptible to environmental factors such as UV light and moisture.
- Soft Hand Feel: They provide a soft hand feel, ensuring comfort when printed on fabrics.
Advantages of Using Silicone Inks for Screen Printing
The use of silicone inks for screen printing presents several advantages that can enhance not just the final product but the overall printing process. Here are some notable benefits:
1. Exceptional Durability
One of the most compelling reasons to choose silicone inks for screen printing is their outstanding durability. Unlike many traditional inks, silicone inks are formulated to withstand various environmental conditions. They resist fading from sunlight, do not degrade easily in water, and can endure multiple wash cycles without losing vibrancy. This quality makes them particularly appealing for apparel intended for long-term use, such as sports jerseys and workwear.
2. Flexible Application
Silicone inks exhibit remarkable flexibility, making them suitable for a variety of fabrics, including stretchy and delicate ones. When printed, they expand and contract with the fabric, ensuring that the print remains intact and does not crack over time. This characteristic is particularly important for performance apparel and activewear.
3. Eco-Friendly Options
As eco-consciousness continues to grow, many manufacturers have developed silicone inks for screen printing that are free from harmful solvents and chemicals. This shift towards sustainability allows businesses to promote their products as environmentally friendly while adhering to stricter regulations and standards. Using silicone inks contributes positively to reducing carbon footprint and supports green manufacturing practices.
4. Reduced Ink Consumption
Silicone inks often require less volume to achieve vibrant colors compared to traditional inks. This efficiency means that businesses can save money on material costs while simultaneously reducing waste. This advantage makes silicone inks a cost-effective choice for screen printing operations looking to optimize their budgets.
5. Versatility Across Substrates
While traditionally used on textiles, silicone inks can be effective on a variety of substrates such as rubber, plastic, and more. This versatility allows screen printers to expand their service offerings, catering to different market needs, which can lead to increased revenue streams.
Applications of Silicone Inks in Screen Printing
Silicone inks are used in many applications across various industries. Here are some common uses:
1. Apparel Printing
Silicone inks for screen printing are widely used in the garment industry for printing on T-shirts, hoodies, sportswear, and more. The flexibility and durability of these inks ensure that prints remain vibrant and intact through countless washes. They are ideal for high-performance athletic gear where comfort and durability are paramount.
2. Promotional Products
From tote bags to caps and wearable items, silicone inks can provide a high-quality finish that enhances brand visibility. The durability of prints on promotional items ensures that logos and messages remain intact for the life of the product, making them an excellent choice for companies looking to promote their brands effectively.
3. Specialized Industries
Certain industries, such as automotive and medical, utilize silicone inks for printing on components and products where durability and safety are essential. For example, silicone inks can be used on labels for outdoor equipment or for printing medical device components that require high levels of cleanliness and stability.
Best Practices for Using Silicone Inks
To get the most out of silicone inks for screen printing, it is crucial to follow best practices. Here are some tips to ensure the best results:
1. Proper Curing
Curing silicone inks effectively is essential to maximize their performance. Unlike water-based inks, silicone requires specific curing times and temperatures to achieve the best adhesion and durability. Be sure to refer to the manufacturer's guidelines for optimal results.
2. Screen Preparation
Before printing, ensure your screens are clean and well-prepared. This will prevent ink buildup and provide a smooth printing process, resulting in clean prints. Consider using a high mesh count for finer designs, as silicone inks are thicker than standard inks.
3. Use Compatible Substrates
Silicone inks adhere best to specially coated textiles and substrates. Ensure that the fabric or material being used is compatible with silicone inks. Conduct tests on sample materials before full production to guarantee the desired results.
4. Experiment with Colors
Silicone inks are available in a wide array of colors and finishes. Don’t hesitate to experiment with mixing inks or layering colors to create unique effects. Remember that the colors may appear differently once cured, so always conduct adjustments and tests.
5. Clean Up and Maintenance
After printing, clean your screens and tools promptly to prevent ink from drying and clogging your equipment. Silicone inks require specific solvents for cleaning, so consult the manufacturer’s recommendations for safe and effective cleaning methods.
The Future of Silicone Inks in Screen Printing
The screen printing industry continues to evolve, and silicone inks are leading the charge towards innovation and sustainability. As technology advances, we may see even more versatile applications and enhanced formulations that expand the capabilities of silicone inks. Businesses that adopt these inks early will position themselves ahead of the curve, gaining a competitive advantage in a fast-paced market.
Conclusion
In conclusion, silicone inks for screen printing represent a significant advancement in the printing industry. Their durability, flexibility, environmental benefits, and versatility make them an excellent choice for a wide range of applications. By adopting best practices and pursuing innovative uses for these inks, businesses can not only enhance their product offerings but also contribute positively to industry sustainability.
For those interested in exploring silicone inks further, it’s beneficial to consult with leading suppliers and experts in the field. As the printing world continues to evolve, staying informed about advancements in materials and techniques will ensure that your business remains at the forefront of the industry.
At Boston Industrial Solutions, we are committed to providing top-notch printing services with the latest technology and products. Reach out to us today to discover how our expertise in silicone inks can elevate your printing projects to new heights!